Q&A: Michelin Resicare on road to RF-free future
3 Jul 2025
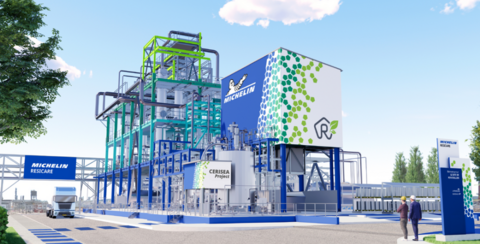
Bio-based tire cord adhesive claimed to be “the fastest-deployed RF-free system on the market…”
Clermont-Ferrand, France – Michelin’s Resicare unit is ramping up efforts to increase demand for its tire cord adhesive – developed as a bio-based and non-toxic alternative to conventionally used RF (resorcinol-formaldehyde) products.
Having reached a milestone with over 100 million tires produced using the resin this year, Clermont-Ferrand-based Resicare is now actively promoting the technology to other major tire manufacturers.
Here, ERJ asks Emeline Chamoux, business development – Resicare, Michelin Engineered Polymers, about the current status of the product and future prospects for its industry-wide adoption:
ERJ: Please describe the programme behind the development of Resicare
EC: In 2006, Michelin's laboratories embarked on a journey to develop a non-toxic, high performance resin solution. This ambition gave birth to Resicare, a dedicated subsidiary to make this innovation accessible to the entire industry, including Michelin's competitors. The results speak for themselves: over 100 million tires have been manufactured using ResiCare resin: marking a major milestone in sustainable tire production.
ERJ: What have been the main technical challenges in developing Resicare for use in tires?
EC: Several years of R&D were needed to find a non-toxic, high-performance, and bio-sourced solution. It was necessary to prove the technical robustness in terms of product performance, industrialisation and economic viability – for use in premium tires today and in the future.
ERJ: Is Resicare a drop-in replacement for RF resins or are modifications needed for the tire cord and/or converting processes?
EC: It's a plug & play technology, meaning that you will reach the same performances in terms of adhesion, peel strength etc, without any changes on the dipping line: we just change the RF part in the traditional RFL (resorcinol formaldehyde latex) solution. This approach ensures a smooth transition to safer chemistry, with minimal disruption to production.
ERJ: How does the cost of Resicare compare with that of conventional RF resin adhesives?
EC: As a premium and disruptive technology, the price is higher in absolute terms. But relatively [the increase in] cost is acceptable (4 cents per tire) and the scale-up effect will optimise the cost in the coming years. While some may be tempted to compare costs per kilogram, this misses the broader value proposition. ResiCare is a premium solution in what it delivers. Traditional RF resins come with hidden costs: regulatory compliance, worker safety measures, and environmental liabilities. European directives like 2004/37 are already pushing manufacturers to reduce formaldehyde exposure. ResiCare anticipates this shift, offering a future-proof alternative that reduces risk and simplifies operations.
ERJ: How does the performance of Resicare compare with conventional RF resin adhesives?
EC: Compared to RF resin, our solution removes all the toxicity generated by formaldehyde and resorcinol (carcinogenic and endocrine perturbator), however since it's a Novalac phenolic resin (an araminolic) it behaves like the ‘old’ generation in terms of performance – sometimes even slightly better. ResiCare's solution, free from SVHC (substances of very high concern) criteria, offers a safer alternative than: formaldehyde, classified as a carcinogen 1B since 2016, and resorcinol, recognised as a category 1 endocrine disruptor by EU and REACH regulations.
ERJ: How does Resicare compare with other non-RF tire cord adhesives being introduced into the tire market?
There are a lot of non-RF free solutions appearing on the tire market: showing that the world is moving toward RF-free solutions. Some tire leaders have their own solutions; some others are using external technologies. All RF-free solutions have their advantages and benefits - industrialisation, performance, chemical [safety] etc. Our solution has proven it's robustness by being used in mass production, and does not contain any monomers, such as isocyanates, that fit the criteria to be classified as SVHC in the near future.
ERJ: At which location(s) is Resicare being manufactured?
EC: ResiCare is already fully deployed at industrial-scale across Europe and Asia and has been validated by five major converters: allowing an international network with production at eight industrial sites. It has been tested and deployed globally, with strong support from Michelin’s teams to overcome industrialisation and scale-up challenges. Today, ResiCare is not just a viable alternative, it’s the fastest-deployed RF-free system on the market.
ERJ: Resicare is also now introducing Resi4TEX. Where does this product fit into the portfolio?
EC: Resi4TEX is an aromatic aldehyde-, water-based phenolic Novolac resin that does not contain measurable SVHC components, such as formaldehyde, resorcinol, phenol and isocyanates and is projected to transition to a bio-based model by 2027. The ‘araminolic’ chemistry not only matches but often exceeds the performance characteristics required for tire reinforcement, with temperature and fatigue resistance enhanced by forming a 3D network. Also, the latex component contributes flexibility and reactivity with rubbers. This combination enables the bonding of textile reinforcements, , such as PET, polyamides 6 and 66, aramid and rayon, to various types of rubber and textiles.
ERJ: How would you describe the tire industry’s progress to date in transitioning to more sustainable tire cord adhesives?
EC: The tire industry is clearly moving towards RF-free solutions, with many leading manufacturers developing their own alternatives. [Among these products] ResiCare offers a proven, robust solution already in industrial production by Michelin. This milestone of 100 million tires manufactured using ResiCare resin is not just symbolic, it represents a significant environmental achievement. By avoiding the use of approximately 30 tons of formaldehyde, we are paving the way for a safer, more sustainable future in tire manufacturing.
ERJ: Thank you.